(¥°) TULLES AND OTHER NET FABRICS
These products are used for making curtains, bedspreads or similar household furnishings, veils, ladies' garments, in embroidery, etc. They are generally of silk, man-made fibres, cotton or linen.(A) Tulle and other bobbin-net fabrics consist of warp threads with weft threads which twist round each warp thread and run diagonally from selvedge to selvedge, half the weft being inclined in one direction and the other half inclined in the other direction (see Figure 1). These wefts form an open mesh with the warp; the meshes may be in regular hexagonal form, square, or diamond-shaped (Neuville net). Another variety of tulle in hexagonal form (Mechlin net) consists of warp threads and a system of bobbin threads which pass longitudinally between two warp threads only (see Figure 2). 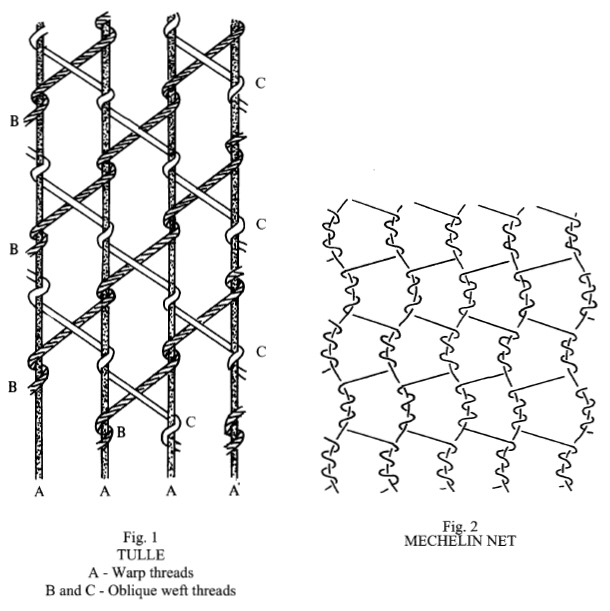 |
(B) Tulle bobinot is a special tulle composed of three series of threads : certain straight parallel warp threads as in ordinary tulle, pattern threads (so called because they produce the pattern) running alternately alongside the straight threads and temporarily away from them to another (usually adjacent) straight thread, thus producing triangular meshes interspersed with spaces of trapezoid or other form, and crossing threads which twist round the straight warp and bind the pattern threads to it (see Figure 3). Opaque parts in the design are produced by grouping together closely a number of such triangular meshes. (C) Net fabrics have three series of threads : parallel warp threads, mesh threads and binding threads (e.g., filet net). Each mesh thread runs alternately alongside different warps forming square meshes as it passes from one to the other. The binding threads hold the fabric together by binding the mesh threads to the warp threads in certain places (see Figure 4). (D) Knotted net fabrics have a uniform square or diamond shaped mesh knotted at each corner so that the threads cannot be pulled apart. They may be hand or machine made. The heading does not include : (a) Loosely woven fabrics of Chapters 50 to 55, and gauze of heading 58.03. (b) Nets or netting of heading 56.08. (c) Bolting cloth (heading 59.11). (d) Knitted or crocheted fabrics of Chapter 60. (e) Tulle and other net fabrics made up as indicated in Part (¥±) of the General Explanatory Note to Section XI. (¥±) LACE Lace is an ornamental or decorative openwork fabric in which design elements (more or less intricate) formed by the intertwisting of threads are joined either by meshes, usually of regular size and shape, forming an apparent openwork ground fabric, or by ornamental links (brides) which themselves give pattern effects. The design elements and background of mesh or brides are usually produced simultaneously but sometimes the design elements are made separately and assembled afterwards. It is an essential characteristic of lace that the design element is not worked on a pre-existing ground. For the purposes of this heading the term therefore does not extend to products of similar appearance and, indeed, sometimes known as lace (e.g. filet lace), made by filling in or decorating the meshes of a pre-existent ground of tulle or net, or by sewn applique work on a ground, whether or not the ground is subsequently wholly or partly removed. Such products are classified as embroidery in heading 58.10, as are also true laces which have been subsequently embroidered, and encrusted lace produced by sewn applique work. The heading also excludes openwork products of any kind produced by knitting by hand or machine (Chapter 60); these can be recognised usually by the characteristic knitting stitch, particularly at the solid parts. Unlike tulles, gauzes or other loosely woven fabrics, lace does not have distinct warp and weft. It is often executed with a single thread and when more than one thread is used it fulfils the same function. Lace may be made by hand or machine. The principal classes of hand-made lace are : (A) Needlepoint lace, executed with a needle on a sheet of paper or parchment bearing the design. The lace follows the outline of the pattern, its component threads lying on the paper but not piercing it; the frame threads, i.e., those forming the initial skeleton of the lace are temporarily attached to the pattern by crossing stitches in order to facilitate the work. Needlepoint lace includes Alencon, Argentan, Venetian, etc. (B) Bobbin lace (pillow lace) worked with several threads wound on bobbins and twisted together on a "pillow" or "cushion" on which the pattern is fastened and in which are temporarily inserted pins to facilitate production of the lace. Bobbin or pillow laces include Valenciennes, Chantilly, Malines, Bruges, Duchesse, Puy, etc. (C) Crochet lace (e.g., that known as Irish crochet lace). Unlike the varieties described above, crochet lace is not laid on a design or support when being made; it is made by hand with a crochet hook. (D) Various other kinds of lace, more or less resembling the other varieties, e.g. : (1) Teneriffe lace, made in the same manner as needlepoint lace. (2) Lacet work, needlepoint lace in which certain parts are obtained by the use of lacet braid; made on a pillow or mechanically. (3) Tatting lace, similar to crochet lace but with round designs and knotted by means of a shuttle. (4) Macrame lace, a heavy lace made by knotting in various ways a series of threads fixed at right angles to a leading thread. Machine-made lace is similar to hand-made lace in general appearance but, except in the case of bobbin laces, the method of interlacing the threads is different and machine-made lace is more uniform than hand-made. Hand or machine made lace is classified here whether : (¥¡) In the piece or in strips of any length. or (¥¢) In the form of motifs, i.e., individual pieces designed solely to be incorporated in, or appliqued on, other articles such as nightdresses, slips, blouses or other articles of apparel, handkerchiefs, table cloths or other furnishings. These goods are classified in this heading whether made directly in one piece by the lace maker, or cut from larger pieces or assembled from several separate lace elements. The heading does not cover articles of lace; these are classified according to their character, generally in Chapter 62 or 63 (e.g., lace mantillas in heading 62.14, lace yokes and collars for women's garments in heading 62.17, and lace table mats in heading 63.04). Subheading Explanatory Note. Subheadings 5804.21, 5804.29 and 5804.30 Mechanically made imitations of hand-made lace, are similar in general appearance to hand-made lace but can be distinguished on the basis of the following criteria : Mechanically made lace is often produced in fairly wide pieces which are cut into strips during the finishing process. In this case, the lace edges of the cut strips nearly always retain the stitches or parts of stitches from the openwork fabric which joined one strip to the next on the loom. These stitches or parts of stitches are found on the outside of the lace. They are usually seen where the line on the edge forms a recessed angle, i.e., where it is difficult to reach them without at the same time destroying the edge itself. The presence of these stitches or parts of stitches is a clear indication that the lace is mechanically made. A distinction can also be made by examination of the decorative motifs of the lace, the flow of the relief (or contour) threads and of the filling-in threads. In hand-made lace, these threads can run in any direction and may in fact be returned to their original direction. In mechanically made lace, such reverse stitching is not possible; these threads can therefore slant to the right or to the left, but they must follow the progressive direction of the work. The method of filling in the opaque parts of the design is a third factor to be borne in mind in distinguishing between hand-made lace and mechanically made lace. In hand-made lace, only the following are used : - the lock-stitch, i.e., the scallop stitch or buttonhole stitch if it is needlepoint lace - the cloth or gate stitch if it is bobbin lace. The cloth stitch reproduces exactly the plain weave. In a gate stitch, the threads serve as warp threads and are divided into two superimposed series which between them form an angle of approximately 90¨¬; the weft thread passes across this surface, passing alternately on top of one thread of the first series (top series) and under the thread(s) of the second series immediately following. In mechanically made lace, the most widely used methods of filling are as follows : - the cloth stitch, but with one peculiarity in that the threads which form the weft do not necessarily run from one edge of the design to the other. In some cases, they run only part of the way across and another thread meets the first to complete the section; - a method of mounting similar to that used in obtaining the full parts in tulle bobinot (straight threads, pattern threads, tie threads); - inserting through the net, a thread which forms with the warp threads a plain weave. In the above two procedures, the net ends at the point where the design begins, but this is not so in this case. The following considerations can also help to distinguish hand-made lace from mechanically made lace. Indeed, in some cases such considerations provide the only means by which a distinction can be made, particularly when distinguishing between hand-made bobbin lace and mechanically made bobbin lace : (a) Small faults or imperfections found in hand-made lace are irregularly spaced and are rarely similar in appearance, whereas in mechanically made lace they are repeated regularly, due to the action of the mechanical device used in their manufacture. (b) The picot loops which often trim the edges of hand-made lace are always formed by the threads which make up the net, whereas they are sometimes added to mechanically made lace. In such cases they are much less firmly attached and can be pulled away without destroying the lace itself. This is not possible with hand-made lace. (c) The method of dispatch and packing is also a means of distinguishing hand-made lace from mechanically made lace. Hand-made lace is not usually dispatched in lengths greater than 20 metres, and each piece in a consignment is generally of a different pattern. Mechanically made lace is always longer and may be as much as 500 metres in length; such consignments always include a considerable number of pieces of the same pattern. In addition there is "mixed" lace, known as lacet lace, renaissance lace, Luxeuil lace and princess lace. The manufacture of such lace begins from a lacet (braid) obtained mechanically, which is laid flat on a tracing and follows the lines of the design. At the angles the braid is folded again so as to follow the tracing; the parts which overlap are sewn together; the ends of the cut braids are delicately sewn into place. The loops and filling-in stitches are then made with the needle. In addition to the fact that the braid has been folded over, cut, and sewn as described above, such lace may sometimes be recognised by the gathers in the braid on the concave edges of the design. This lace is regarded as hand-made lace.
|